Operations can be started and stopped two ways; using the menus in the application or scanning barcodes on printouts. Both ways results in the same functionality being triggered, the below describes the menus in the application.
Start Operation
This starts the operation. When selected a dialog is displayed where the user can select to start the Setup Time or the Run Time (note that if only one of the two are setup to be captured in the Mobile Manufacturing Time Capture Setup table, then the selection dialog is not displayed).
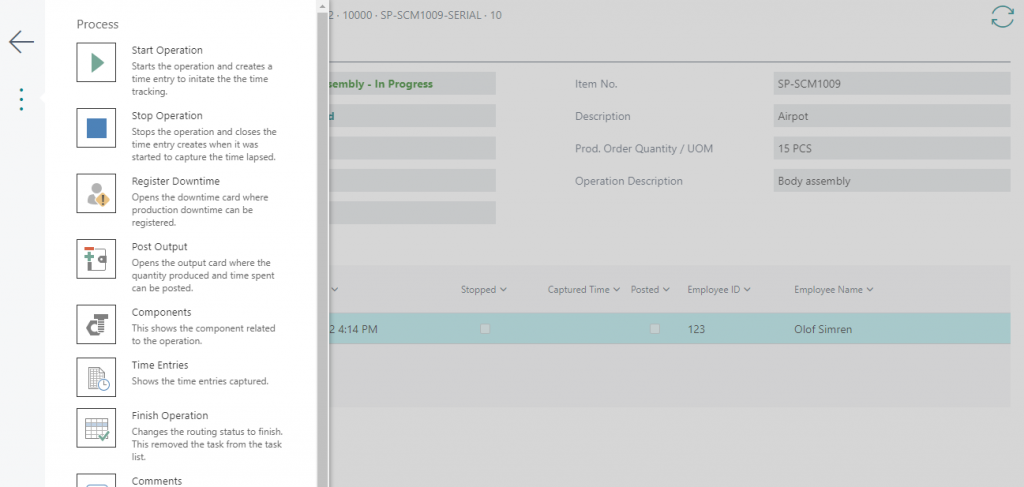
When an operation is started the system will set the Routing Status of the operation to In Progress and will create a Time Entry record to log that the operation was started. If the Run Time was already started and the user starts the Setup Time, then the Run Time will be stopped automatically if Multiple Starts are not allowed according to the Mobile Manufacturing Time Capture Setup. The details of the time entries are described in the Time Entry section.
Stop Operation
This stops the operation. When selected the system will find the oldest started Time Entry and create a related Time Entry record to log that the operation was stopped. At this point the Captured Time of the Mobile Manufacturing Time Entry is calculated and update on the Start Entry. The Captured Time represents how long the operation took and can be used when posting the output. The Posted field on the Mobile Manufacturing Time Entries indicates if the entry been used for posting output or not.